تولید آهن زنگ نزن فرایندی پیچیده و دقیق است که با ذوب مواد اولیه آغاز میشود. در این مرحله، آهن خام با عناصر آلیاژی نظیر کروم و نیکل ترکیب میشود. این ترکیب به کمک کورههای قوس الکتریکی به دمای بالا میرسد تا ذوب کامل شود. پس از ذوب، مواد به قالبهای مشخصی ریخته و به شکلهای مختلفی تبدیل میشوند. سپس نوبت به عملیات حرارتی میرسد که موجب بهبود خواص مکانیکی و افزایش مقاومت به زنگزدگی میشود. سطح آهن زنگ نزن با روشهای مختلفی نظیر پولیش و پرداخت، آماده مصرف میگردد. بر همین اساس در ادامه از مجموعه ساپراویسمن به بررسی مراحل تولید آهن زنگ نزن خواهیم پرداخت.
فهرست مطلب
Toggleآهن زنگ نزن چیست؟
آهن زنگ نزن که به عنوان استنلس استیل نیز شناخته میشود، یکی از شگفتانگیزترین آلیاژهای فلزی است که به دلیل ویژگیهای منحصر به فردش در صنایع مختلف محبوبیت فراوانی دارد. این آلیاژ عمدتاً از آهن، کروم و نیکل تشکیل شده و خاصیت ضد زنگزدگی آن ناشی از وجود کروم در ترکیبش است. وقتی کروم با اکسیژن هوا واکنش میدهد، لایهای محافظ روی سطح فلز ایجاد میکند که از خوردگی جلوگیری میکند.
یکی از دلایل جذابیت آهن زنگ نزن، زیبایی و درخشندگی آن است. این ویژگی در مراحل تولید آهن زنگ نزن باعث میشود که در طراحیهای مدرن و لوکس، از وسایل آشپزخانه گرفته تا مبلمان و دکوراسیون داخلی، به کار رود. علاوه بر این، دوام و مقاومت بالای آن در برابر حرارت و فشار، آن را به انتخابی ایدهآل برای صنایع غذایی و پزشکی تبدیل کرده است.
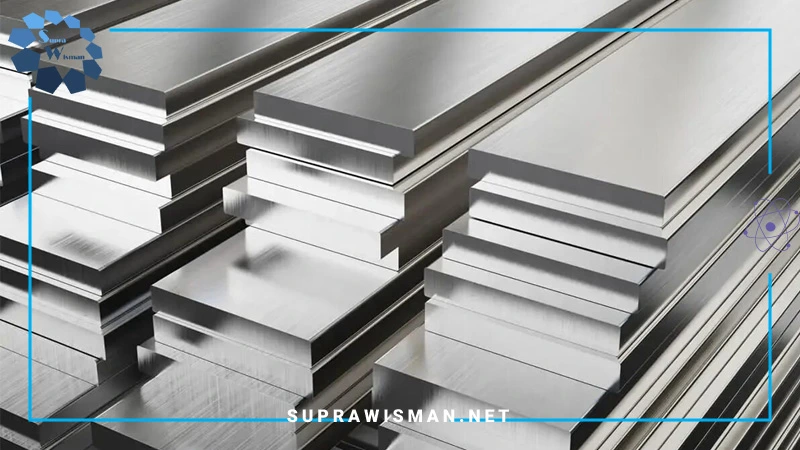
مراحل تولید آهن زنگ نزن چیست؟
مراحل تولید آهن زنگ نزن
آهن زنگ نزن از مواد پرکاربرد در صنایع مختلف است که به دلیل مقاومت بالا در برابر زنگزدگی و خوردگی، توجه بسیاری را به خود جلب کرده است. مراحل تولید آهن زنگ نزن شامل مراحل مختلفی است که در ادامه به توضیح آنها میپردازیم.
ذوب و ریختهگری
اولین مرحله در تولید آهنهای زنگ نزن، ذوب و ریختهگری مواد اولیه است. در این مرحله، ترکیب دقیق فلزات و عناصر مختلف مانند کروم، نیکل و مولیبدن به منظور ایجاد آلیاژ مقاوم در برابر زنگزدگی انجام میشود. پس از تعیین ترکیب مناسب در مراحل تولید آهن زنگ نزن، مواد در کورههای مخصوص ذوب میشوند. این فرآیند نیازمند دمای بسیار بالا و کنترل دقیق شرایط است تا آلیاژ تولیدی دارای ویژگیهای مورد انتظار باشد. در فرآیندهای ریختهگری و شکلدهی آهن زنگ نزن، مشابه با استفاده از برد سرامیکی نسوز، مواد مذاب به دقت در قالبها ریخته میشوند تا از آسیبدیدگی و اختلالات حرارتی جلوگیری شود.
پس از ذوب، فلز مذاب به قالبهای مخصوص ریخته میشود تا به شکلهای مختلف تبدیل گردد. این مرحله نیازمند دقت بالا و تکنولوژی پیشرفته است تا محصول نهایی بدون نقص و با کیفیت بالا تولید شود. در مراحل تولید آهن زنگ نزن، مشابه به استفاده از سرامیک فایبر برای عایقبندی کورههای صنعتی، دماهای بالا در کورههای ذوب آهن برای ذوب مواد اولیه کنترل میشود.
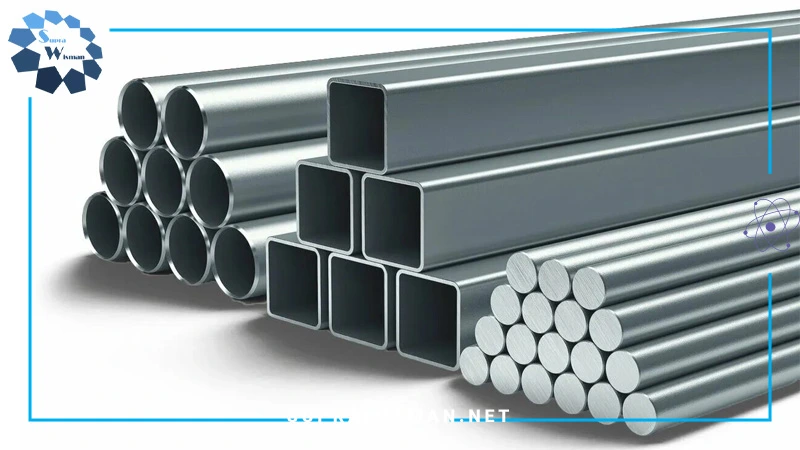
بررسی مراحل تولید آهن زنگ نزن
شکل دادن
پس از ریختهگری در مراحل تولید آهن زنگ نزن، آهن زنگ نزن وارد مرحله شکل دادن میشود. در این مرحله، فلز به شکلهای مختلفی مانند ورق، لوله و میله تبدیل میشود. فرآیند شکلدهی میتواند شامل نورد گرم و سرد، اکستروژن و فرفورژه باشد. هر یک از این روشها ویژگیها و مزایای خاص خود را دارند و بسته به نیاز صنایع مختلف انتخاب میشوند.
محصولات تولیدی تحت فرآیندهای تکمیلی مانند پرداخت و پوششدهی قرار میگیرند تا خواص سطحی بهبود یابد و آمادهی استفاده در صنایع مختلف شوند. این مراحل تضمین میکنند که آهن زنگ نزن تولیدی همواره کیفیت و دوام بالایی داشته باشد.
حرارت دادن
حرارت دادن از اصلیترین مراحل تولید آهن زنگ نزن است که نقش بسزایی در بهبود خواص مکانیکی و شیمیایی این آلیاژ دارد. در این فرآیند، با استفاده از دماهای بالا، ساختار میکروسکوپی آهن زنگ نزن تغییر میکند و به این ترتیب، ویژگیهایی همچون مقاومت در برابر خوردگی و استحکام آن افزایش مییابد.
این مرحله در روش های تولید آهن زنگ نزن به طور معمول در کورههای مخصوص انجام میشود که دما میتواند به 1000 درجه سانتیگراد یا بیشتر برسد. حرارت دادن باعث میشود تا ذرات آلیاژ به حالت یکنواختتری درآیند و تنشهای داخلی کاهش یابد. همچنین این فرآیند به تسهیل در شکلدهی و ماشینکاری آهن زنگ نزن کمک میکند. در مراحل مختلف حرارتدهی آهن زنگ نزن، از پتو نسوز سرامیکی بهعنوان عایقهای حرارتی برای حفظ دما و تضمین یکنواختی ساختار میکروسکوپی استفاده میشود
مراحل تولید آهن زنگ نزن باعث تولید محصولاتی با کیفیت بالا و عمر طولانی است که در صنایع مختلف از جمله ساخت و ساز، خودروسازی و تجهیزات پزشکی کاربرد دارند. بنابراین، حرارت دادن نه تنها یک مرحله ضروری در تولید آهن زنگ نزن است، بلکه به عنوان یک عامل تعیینکننده در کیفیت و عملکرد نهایی محصولات شناخته میشود. در فرآیندهای حرارتی مانند سختکاری آهن زنگ نزن، استفاده از الیاف سرامیکی در عایقهای حرارتی میتواند به بهبود کیفیت نهایی محصول و کاهش اتلاف انرژی کمک کند.
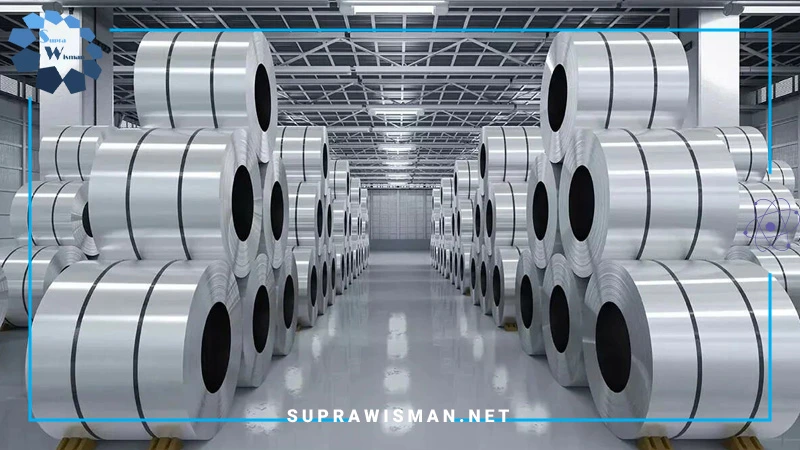
انواع مراحل تولید آهن زنگ نزن
رسوبزدایی
آهن زنگ نزن جزو پرکاربردترین آلیاژها در صنایع مختلف است که به دلیل مقاومت بالا در برابر خوردگی و استحکام بینظیرش شناخته میشود. مراحل تولید این آلیاژ جذاب و پیچیده است. در مرحله رسوب زدایی برای تولید این آهن، ناخالصیها و مواد زائد از مایع آهن جدا میشوند تا خلوص آن به حداکثر برسد. این مراحل تولید آهن زنگ نزن بهویژه برای تولید آلیاژهایی که قرار است در محیطهای خورنده و سخت استفاده شوند، اهمیت دارد.
در طول ذوب آهن، مواد مختلفی به شکل ناخالصی وارد مایع میشوند. رسوبزدایی با استفاده از روشهای شیمیایی و فیزیکی انجام میشود؛ بهطوریکه با افزودن مواد خاصی، این ناخالصیها به صورت رسوبات جدا میشوند. سپس، این رسوبات از مایع خارج شده و تنها آهن خالص باقی میماند. این مرحله نهتنها باعث افزایش مقاومت در برابر خوردگی میشود، بلکه خواص مکانیکی آهن زنگ نزن را نیز بهبود میبخشد.
سختکاری
در مراحل تولید آهن زنگ نزن تحت دماهای بالا قرار میگیرد و سپس به سرعت سرد میشود. این تغییر دما باعث میشود که ساختار کریستالی فلز تغییر کند و خواص آن بهبود یابد. نتیجه این فرآیند، افزایش سختی و استحکام آهن زنگ نزن است که آن را برای استفاده در شرایط سخت و محیطهای خورنده مناسب میکند. بهعنوان مثال، در صنایع غذایی، پزشکی و خودروسازی، کیفیت و دوام مواد استفاده شده از اهمیت ویژهای برخوردار است.
سختکاری به این آلیاژ کمک میکند تا در برابر خراشیدگی و خوردگی مقاومت بیشتری داشته باشد. این مرحله نهتنها به زیبایی ظاهری آهن زنگ نزن کمک میکند، بلکه عمر مفید آن را نیز افزایش میدهد. بنابراین مراحل تولید آهن زنگ نزن، رسختکاری نهتنها یک فرآیند فنی، بلکه یک هنر در تولید آلیاژهای باکیفیت است که تأثیر عمیقی بر زندگی روزمره ما دارد.
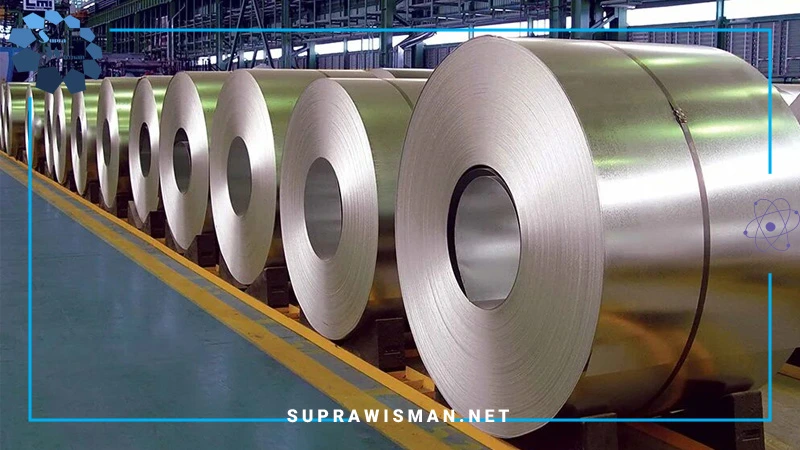
روش های مراحل تولید آهن زنگ نزن
برش یا ماشینکاری
این فرآیند به ما امکان میدهد تا آلیاژهای باکیفیت و دقیق را به اشکال و اندازههای مورد نیاز تبدیل کنیم. در این مرحله، ابزارهای پیشرفته و فناوریهای نوین به کار گرفته میشوند تا برشهای تمیز و دقیقی ایجاد شود. ماشینکاری در مراحل تولید آهن زنگ نزن نهتنها به افزایش دقت ابعاد کمک میکند، بلکه کیفیت سطح نهایی را نیز بهبود میبخشد. این ویژگیها باعث میشوند که آهن زنگ نزن در صنایع مختلف، از خودروسازی گرفته تا تجهیزات پزشکی، به یک انتخاب ایدهآل تبدیل شود.
با استفاده از تکنیکهای مدرن مانند CNC (کنترل عددی رایانهای)، میتوان برشهایی با دقت میلیمتری ایجاد کرد که در نهایت منجر به تولید محصولاتی با عمر طولانی و عملکرد عالی میشود. همچنین ماشینکاری به ما این امکان را میدهد که خلاقیت خود را در طراحی و تولید به کار بگیریم و محصولاتی منحصر به فرد و با کیفیت بالا ارائه دهیم.
جمع بندی
در این مقاله از مجموعه ساپراویسمن به بررسی مراحل تولید آهن زنگ نزن پرداختیم. همچنین در این مقاله به بررسی چیستی آهن زن نزن نیز پرداخته شد. شایان ذکر است، شما میتوانید برای دریافت اطلاعات بیشتر در رابطه با این موضوع با مشاوران حرفهای مجموعه گئومات ارتباط حاصل فرمایید.
شرکت ساپراویسمن
سوالات متداول
- آهن زنگ نزن چگونه تولید میشود و چه موادی در آن استفاده میشود؟
تولید آهن زنگ نزن (استنلس استیل) به فرآیندهای خاصی نیاز دارد. این آلیاژ عمدتاً از آهن، کروم (حداقل 10.5 درصد) و نیکل تشکیل شده است. مراحل تولید از استخراج مواد اولیه آغاز میشود. آهن و کروم از معادن استخراج شده و سپس به کورههای ذوب منتقل میشوند. در این کورهها، با حرارت بالا، این مواد ذوب و ترکیب میشوند تا آلیاژ استنلس استیل به دست آید.
- آیا فرآیند تولید آهن زنگ نزن شامل مراحل خاصی برای بهبود کیفیت است؟
مراحل تولید آهن زنگ نزن شامل مراحل متعددی است که به بهبود کیفیت آن کمک میکند. پس از ذوب، مذاب به شکلهای مختلفی ریختهگری میشود. سپس، این قطعات تحت فرآیندهای ماشینکاری و برش دقیق قرار میگیرند تا به ابعاد و اشکال مورد نظر برسند. در نهایت، مراحل پولیش و پرداخت سطح انجام میشود تا نه تنها زیبایی محصول افزایش یابد بلکه مقاومت آن در برابر زنگزدگی و خوردگی نیز بهبود یابد.
- چرا آهن زنگ نزن برای صنایع مختلف محبوب است؟
آهن زنگ نزن به دلیل ویژگیهای منحصر به فردش، مانند مقاومت بالا در برابر زنگزدگی و خوردگی، بسیار محبوب است. این آلیاژ به راحتی تمیز میشود و ظاهری براق و زیبا دارد که آن را برای استفاده در صنایع غذایی، پزشکی و ساختمانی ایدهآل میکند. همچنین در مراحل تولید آهن زنگ نزن، دوام و طول عمر بالای آن باعث کاهش هزینههای تعمیر و نگهداری میشود، که این خود یکی از دلایل اصلی محبوبیت آن در بازار است.
هنوز کسی نظری نداده! اولین نفر باش...