قالبگیری تزریقی سرامیک، فناوری نوینی است که تحولات زیادی در عرصه تولید قطعات صنعتی ایجاد کرده است. این روش پیشرفته امکان ساخت قطعات پیچیده با دقت بالا و کیفیت مطلوب را فراهم میکند. از الکترونیک گرفته تا پزشکی، صنایع مختلف از مزایای این تکنولوژی بهره میبرند. سرامیکها با خواص منحصر به فرد خود مانند مقاومت بالا، پایداری حرارتی و مقاومت شیمیایی، گزینهای استثنایی برای تولید قطعات پیشرفته محسوب میشوند.
فهرست مطلب
Toggleهمچنین، الیاف سرامیکی که در این فرآیند استفاده میشوند، به دلیل خواص مقاومت حرارتی و مکانیکی، استحکام و دوام قطعات تولید شده را بهبود میبخشند. قالبگیری تزریقی راهکاری نوآورانه است که پتانسیل مواد سرامیکی را به حداکثر میرساند و امکان تولید محصولاتی با کارایی بالاتر و دقت بیشتر را میسر میسازد.
قالب گیری تزریقی سرامیک از کجا آمد؟
تکنولوژی قالب گیری تزریقی سرامیک (CIM)، ریشه در دهه ۱۹۳۰ دارد، اما شکوفایی واقعی آن در دهههای ۱۹۷۰ و ۱۹۸۰ رخ داد. در ابتدا این فناوری برای تولید قطعات سرامیکی با اشکال پیچیده و دقیق طراحی شد. با پیشرفتهای تکنولوژیکی، این روش به تدریج به یکی از روشهای اصلی تولید قطعات سرامیکی پیچیده تبدیل شد. در دهه ۱۹۸۰، تمرکز اصلی بر تولید قطعات سرامیکی غیر اکسیدی با دمای بالا مانند نیترید سیلیکون و کاربید سیلیکون بهویژه برای کاربردهای صنعتی مانند روتورهای توربین در خودروهای مسابقهای و وسایل نقلیه نظامی بود.
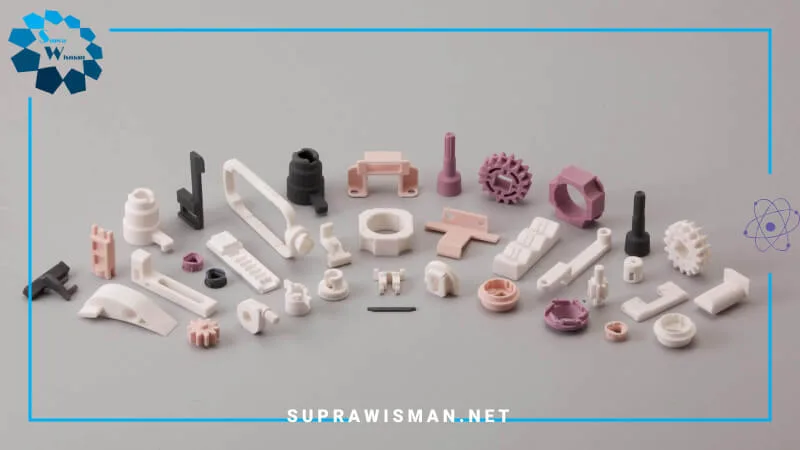
در مورد قالبگیری تزریقی سرامیک چه میدانید؟
مواد سرامیک مورد استفاده و کاربردهای آنها
سرامیکها مواد مهندسی پیشرفتهای هستند که از ترکیبات غیرآلی با پیوندهای یونی یا کووالانسی تشکیل شدهاند و دارای ویژگیهای مهمی مانند مقاومت بالا، سختی، پایداری حرارتی و مقاومت شیمیایی هستند. با پیشرفت فناوری قالب گیری تزریقی سرامیک (CIM)، امکان تولید انواع پیشرفته سرامیکها با دقت بالا و کاربردهای متنوع فراهم شده است.
آلومینا (Al2O3)
آلومینا یکی از پرکاربردترین مواد سرامیکی است که به دلیل مقاومت مکانیکی بالا، مقاومت سایشی عالی و پایداری حرارتی گسترده مورد استفاده قرار میگیرد. در صنایع الکترونیک به عنوان زیرلایه مدارهای مجتمع، در صنایع پزشکی برای ساخت پروتزها و در صنایع مهندسی برای تولید قطعات مقاوم به سایش، کاربرد دارد.
زیرکونیا (ZrO2)
زیرکونیا، سرامیکی با چقرمگی بالا و مقاومت مکانیکی فوقالعاده است. این ماده در ساخت تیغههای توربین، قطعات موتور، ابزارهای برشی و کاشتهای پزشکی مانند مفاصل مصنوعی استفاده میشود. مقاومت به خوردگی و پایداری حرارتی از دیگر ویژگیهای منحصر به فرد زیرکونیا است.
کاربید سیلیکون (SiC)
کاربید سیلیکون سرامیکی با مقاومت بالا در برابر دماهای بالا و خوردگی است. این ماده در صنایع هوافضا، قطعات موتور، سنسورها و ابزارهای برشی کاربرد گستردهای دارد. مقاومت به شوک حرارتی و ضریب انبساط پایین از مزایای اصلی این سرامیک است.
نیترید سیلیکون (Si3N4)
نیترید سیلیکون سرامیکی با مقاومت بالا و وزن سبک است که در ساخت قطعات مهندسی پیشرفته مانند یاتاقانها، قطعات توربین و تجهیزات صنعتی استفاده میشود. این ماده مقاومت به خوردگی و پایداری حرارتی بالایی دارد.
تیتانات باریم (BaTiO3)
یک سرامیک پیزوالکتریک است که در ساخت سنسورها، اکچویترها و قطعات الکترونیکی مانند خازنهای سرامیکی کاربرد دارد. این ماده قابلیت تبدیل انرژی مکانیکی به الکتریکی و برعکس را دارد.
هیدروکسی آپاتیت (Ca10(PO4)6(OH)2)
این سرامیک زیستسازگار در کاربردهای پزشکی و دندانپزشکی مانند ترمیم استخوان، کاشتهای دندانی و پوششهای بیومتریال استفاده میشود. ساختار شیمیایی آن شبیه به بافت استخوانی انسان است.
نیترید آلومینیوم (AlN)
نیترید آلومینیوم یک سرامیک با هدایت حرارتی بالا است که در الکترونیک، بهویژه در ساخت مدارهای مجتمع و قطعات الکترونیکی با نیاز به مدیریت حرارت کاربرد دارد.
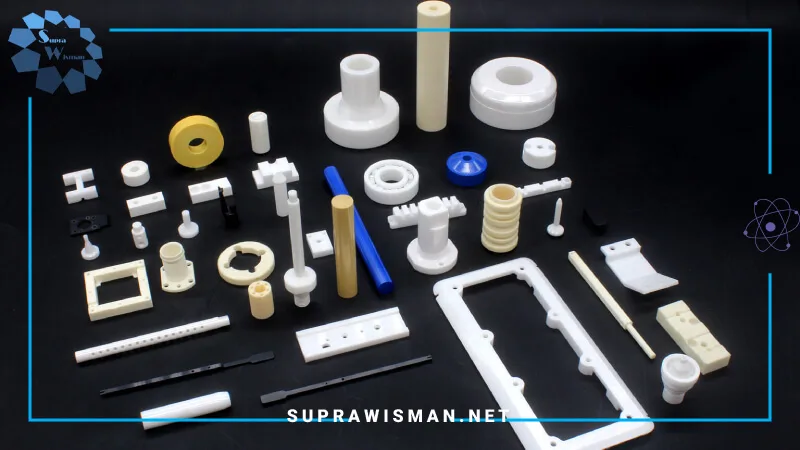
انواع فرآیند قالبگیری تزریقی
طبقهبندی و انواع فرآیند قالبگیری تزریقی
فرآیند قالبگیری تزریقی یکی از مهمترین روشهای تولید قطعات پلاستیکی است که دارای انواع مختلفی میباشد:
- قالبگیری تزریقی استاندارد: رایجترین نوع این فرآیند است که در آن مواد پلاستیکی مذاب با فشار بالا درون قالب فلزی تزریق میشوند. این روش برای تولید انبوه قطعات با دقت بالا و سطح صافی مناسب کاربرد دارد.
- قالبگیری تزریقی گازی: یک روش پیشرفته است که در آن از گاز برای ایجاد حفره یا هسته داخل قطعه پلاستیکی استفاده میشود. این تکنیک امکان تولید قطعات توخالی با دیواره نازک و وزن کم را فراهم میکند و اغلب در صنایع خودروسازی و تولید قطعات پلاستیکی حجیم کاربرد دارد.
- قالبگیری تزریقی: این طبقه بندی با درجه حرارت بالا برای مواد پلاستیکی با نقطه ذوب بالا طراحی شده است. در این روش دمای تزریق و قالب بسیار بالاتر از روشهای معمولی است و امکان شکلدهی به مواد مهندسی پیشرفته را فراهم میکند.
- قالبگیری تزریقی ترکیبی: یک روش پیچیده است که امکان استفاده از چند نوع مواد پلاستیکی با خواص متفاوت در یک قطعه را میسر میسازد. این روش برای تولید قطعات پیچیده با ویژگیهای مکانیکی و فیزیکی خاص مورد استفاده قرار میگیرد.
- قالبگیری تزریقی با فشار پایین: این نوع فرآیند روشی است که برای مواد پلاستیکی ظریف و حساس به کار میرود. در این متد، فشار تزریق کمتر است تا از آسیب دیدن مواد جلوگیری شود و برای تولید قطعات دقیق و ظریف مناسب است.
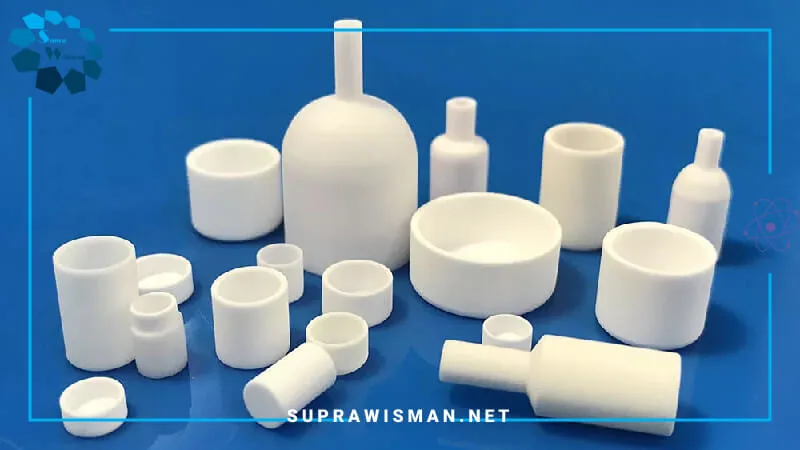
روش کار در قالبگیری تزریقی سرامیک (CIM)
چرخه فرآیند در قالبگیری تزریقی سرامیک (CIM)
چرخه فرآیند CIM عمدتا شامل چهار مرحله اصلی است:
- مرحله اول، تهیه خوراک تزریق است که شامل مخلوط کردن، خشک کردن و دانهبندی پودر سرامیک با حامل آلی مناسب در دمای معین میشود.
- در مرحله دوم، مخلوط تزریق، گرم شده و به مذابی چسبناک تبدیل میشود، سپس با سرعت بالا و تحت دما و فشار معین به درون قالب فلزی تزریق میگردد تا به بدنه سبز موردنظر تبدیل شود.
- مرحله سوم، چربیزدایی است که در آن مواد آلی موجود در بدنه تزریقی با حرارت دادن یا روشهای فیزیکی و شیمیایی حذف میشوند.
- در مرحله نهایی، تفجوشی (سینترینگ) انجام میشود که طی آن روکش سرامیکی بدون چربی در دمای بالا فشرده و پخت میشود تا شکل، دقت اندازه و ریزساختار موردنظر حاصل شود.
سیستمهای بایندر و مفهوم دیبایندینگ
سیستم بایندر یک مؤلفه حیاتی در فرآیند قالب گیری تزریقی سرامیک است. این سیستم شامل یک چسب اصلی، چسب فرعی، عامل پلاستیفایر (نرمکننده) و در برخی موارد شامل مواد سختکننده و فعالکننده سطح برای بهبود خیسشوندگی ذرات میباشد.
به فرآیند حذف یا کاهش مواد چسباننده (بایندر) از قطعه سرامیکی قبل از مرحله پخت نهایی دیبایندینگ گفته میشود. چسب فرعی در دماهای پایینتر سوخته و کانالهایی برای خروج چسب اصلی ایجاد میکند. چسب اصلی تا قبل از سوختن کامل، به قطعه استحکام میدهد. این فرآیند بسیار حساس است و بر کیفیت نهایی قطعه سرامیکی تاثیر مستقیم دارد. مواد بایندر شامل مواد ترموپلاستیک، ترموست و محلولهای آبی با مقادیر کم مواد آلی هستند.
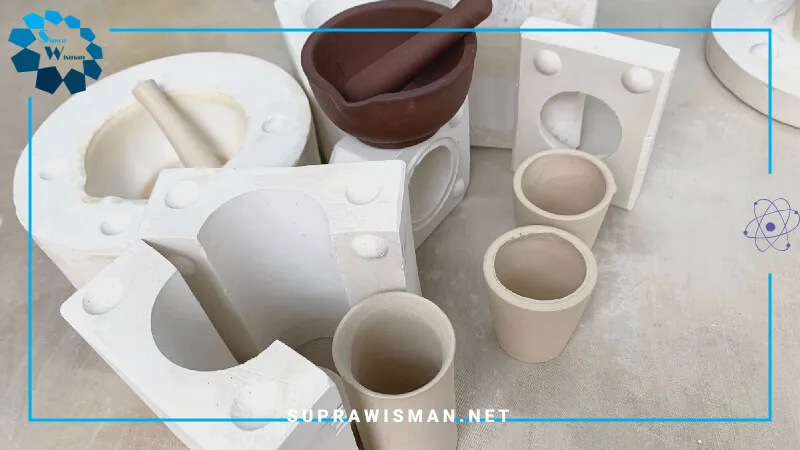
بررسی پارامترهای فرآیند قالبگیری تزریقی
پارامترهای فرآیند قالبگیری تزریقی
پارامترهای اصلی فرآیند قالبگیری تزریقی عبارتنداز:
کنترل کیفیت
کنترل کیفیت در فرآیند قالبگیری تزریقی فرآیندی جامع و چندمرحلهای است که از ابتدای تولید تا پایان محصول را شامل میشود. این روند شامل بازرسیهای دقیق و سیستماتیک در مراحل مختلف تولید میباشد که هدف اصلی آن اطمینان از کیفیت، استاندارد و عملکرد قطعات تولیدی است. این فرآیند شامل نمونهبرداری تصادفی، اندازهگیریهای دقیق با ابزارهای پیشرفته مانند میکرومتر و دستگاههای CMM، بررسی نقایص داخلی با روشهای رادیوگرافی و آلتراسونیک و تحلیل آماری نتایج میباشد. هدف نهایی کنترل کیفیت، حذف یا کاهش حداکثری نقایص، افزایش راندمان تولید، کاهش ضایعات و تضمین رضایت مشتری است.
دمای سیلندر (بشکه)
دمای سیلندر یکی از پارامترهای کلیدی در فرآیند قالبگیری تزریقی است. کنترل دقیق این دما برای تضمین کیفیت محصولات پلاستیکی ضروری است. این دما به عواملی مانند دمای مذاب، سرعت پیچ، فشار برگشتی، حجم تزریق و چرخه قالبگیری بستگی دارد. سیلندر معمولا به مناطق مختلفی تقسیم میشود که هر منطقه میتواند دمای متفاوتی داشته باشد.
دمای مواد مذاب
دمای مواد مذاب نقش مهمی در جریان و عملکرد مواد پلاستیکی دارد. برخلاف مواد فلزی که نقطه ذوب دقیقی دارند، پلاستیکها دارای محدوده دمایی ذوب هستند. این موضوع به دلیل ساختار و ترکیب متفاوت زنجیرههای مولکولی است. برخی مواد مانند PC و PPS در دماهای بالاتر رفتار متفاوتی نشان میدهند، در حالی که موادی مانند PA، PP و PE رفتار پیچیدهتری دارند.
دمای قالب
دمای قالب تاثیر عمیقی بر کیفیت نهایی محصول دارد. برخی مواد پلاستیکی به دلیل دمای کریستالیزاسیون بالا و سرعت تبلور کند، به دمای قالب بالاتری نیاز دارند. دمای قالب میتواند بر ظاهر، اندازه، تغییر شکل و کیفیت سطح قطعه تأثیرگذار باشد. به عنوان مثال، PC معمولا به دمای بالای 60 درجه نیاز دارد، در حالی که PPS میتواند به بیش از 160 درجه برای بهبود کیفیت نیاز داشته باشد.
فشار تزریق
فشار تزریق نیرویی است که مذاب پلاستیک را مجبور به پر کردن قالب میکند. این پارامتر بر اندازه، وزن، تغییر شکل و چگالی محصول تأثیر مستقیم دارد. فشار تزریق برای مواد مختلف متفاوت است و میتواند سیالیت مواد را بهبود بخشد. به عنوان مثال، برای موادی مانند PA و PP، افزایش فشار میتواند سیالیت را به طور قابل توجهی بهتر کند. همچنین، فشار تزریق بر براقیت سطح و توانایی پر کردن قالب تأثیرگذار است.
در مجموع، این چهار پارامتر (3 دما + 1 فشار) نقش تعیینکنندهای در موفقیت فرآیند قالبگیری تزریقی دارند و کنترل دقیق آنها برای تولید محصولات با کیفیت بالا ضروری است.
جمع بندی
فناوری قالب گیری تزریقی سرامیک، پلی میان علم مواد و مهندسی تولید است که چشمانداز جدیدی از ساخت قطعات پیشرفته را گشوده است. این روش با قابلیت تولید قطعات دقیق و پیچیده از انواع مختلف سرامیک، راهگشای نوآوریهای صنعتی در حوزههای گوناگون است. از کاربردهای پزشکی گرفته تا صنایع الکترونیک و هوافضا، قالب گیری تزریقی سرامیک توانسته است محدودیتهای پیشین در تولید را درنوردد و افقهای جدیدی را پیش روی مهندسان و طراحان قرار دهد.
ساپرا ویسمن
سوالات متداول
- قالب گیری تزریقی سرامیک چیست؟
روشی نوین برای تولید قطعات پیچیده سرامیکی با دقت بالا و کیفیت مطلوب است که در صنایع مختلف کاربرد دارد. - مهمترین کاربردهای سرامیک در صنعت کدامند؟
سرامیک در صنایع پزشکی، الکترونیک، هوافضا و مهندسی برای ساخت قطعات مقاوم و دقیق استفاده میشود. - مراحل اصلی قالبگیری تزریقی سرامیک چیست؟
شامل چهار مرحله تهیه خوراک، تزریق، چربیزدایی و تفجوشی است که هر مرحله نقش مهمی در کیفیت نهایی محصول دارد. - مهمترین مزایای قالب گیری تزریقی سرامیک کدامند؟
تولید قطعات با دقت بالا، کیفیت مطلوب، قابلیت شکلدهی پیچیده و استفاده از انواع سرامیکهای مهندسی با خواص منحصر به فرد. - چه نوع سرامیکهایی در این روش کاربرد دارند؟
آلومینا، زیرکونیا، کاربید سیلیکون، نیترید سیلیکون، تیتانات باریم و هیدروکسی آپاتیت از مهمترین سرامیکهای مورد استفاده هستند.
هنوز کسی نظری نداده! اولین نفر باش...