استیل ضد زنگ (فولاد زنگنزن) نوعی فولاد آلیاژی است که حداقل 10.5 درصد کروم دارد و به دلیل این ویژگی، مقاوم به خوردگی و زنگزدگی است. این فولاد علاوه بر کروم، ممکن است شامل عناصری همچون نیکل، مولیبدن، منگنز و سیلیسیم باشد که خواص مختلفی مانند مقاومت به حرارت و استحکام را به فولاد میبخشند. در ادامه همراه ما باشید به بررسی کامل مراحل و روش تولید فولاد ضد زنگ بپردازیم.
فهرست مطلب
Toggleروش تولید فولاد ضد زنگ
تولید این نوع آلیاژها با ذوب ضایعات آهنی شروع و سپس با افزودن عناصر آلیاژی و تعیین ترکیب شیمیایی آن، گرید آلیاژی مشخص میشود. به عبارتی ابتدا مواد خام، قراضه های آهنی یا فولاد ضد زنگ بازیافت شده و در یک کوره قوس الکتریکی با ظرفیتی بالغ بر ۱۶۰ تن تبدیل به مذاب میشود. سپس فلز مذاب به یک مبدل منتقل میشود که برای حصول ترکیب شیمیایی مورد نظر، عناصر آلیاژی به آن اضافه گردد. آلیاژ مذاب در طول فرآیند ریخته گری، به صورت پیوسته ریخته گری، سرد و منجمد میشود.
در این مرحله عرض حداکثری برای ورقها مشخص میشود و سپس رولهای استیل ضد زنگ با عرضها و ضخامتهای مختلف آمده اند. پس از آن برای داشتن ورق با ابعاد مختلف میتوان از طریق هوا برش رولها را به ابعاد مورد نظر برید. به ورقه هایی که توسط کارخانه برش داده میشوند، ورق فابریک گویند. این نوع ورق ها عاری از هرگونه تنش و خش است به همین دلیل مورد استقبال بیشتری قرار میگیرند.
همچنین میتوان از نورد گرم برای تولید ورقهایی نازکتر و بلندتر استفاده کرد. ضخامت به تدریج از طریق این فرآیند کاهش مییابد. عملیات حرارتی آنیل نهایتاً خواص مورد نیاز را با توجه به درخواست و نیاز مشتری به ورق استیل میدهد. همچنین با کمک فرآیند نورد سرد، میتوان سطوح ورق استیل را صاف و براق کرد به همین دلیل از ورقهای کار سرد استیل برای کاربردهای زیبایی مانند طراحی دکوراسیون و یا ساخت لوازم منزل استفاده شود.
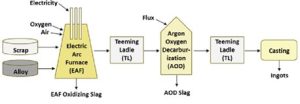
روش تولید فولاد ضد زنگ
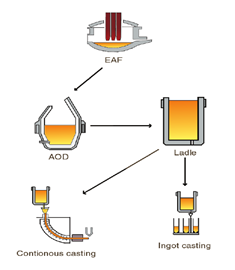
مراحل روش فولاد زنگ نزن
مراحل تولید فولاد ضد زنگ
تولید فولاد زنگ نزن (استنلس استیل) فرآیند پیچیدهای است که شامل مراحل مختلفی از جمله انتخاب مواد اولیه، ذوب و ریختهگری، و فرآیندهای سرد و گرم برای رسیدن به خواص مطلوب فولاد زنگ نزن میشود. فولاد زنگ نزن به دلیل خواص مقاومت به خوردگی و استحکام بالا در صنایع مختلف مورد استفاده قرار میگیرد. در ادامه مراحل تولید فولاد زنگ نزن را شرح میدهیم:
1. انتخاب مواد اولیه:
برای تولید فولاد زنگ نزن از آلیاژهای مختلفی استفاده میشود که معمولاً شامل آهن، کروم، نیکل، منگنز، سیلیسیم و مولیبدن هستند. مقدار کروم در فولاد زنگ نزن معمولاً حداقل 10.5 درصد است، که به آن خواص ضد زنگ میبخشد.
2. ذوب مواد:
فرآیند ذوب فولاد زنگ نزن معمولاً در کورههای قوس الکتریکی یا کورههای القائی انجام میشود. در این مرحله، مواد اولیه (آهن اسفنجی، قراضه فولادی و آلیاژهای دیگر) ذوب میشوند و آلیاژهای مختلف به آن اضافه میشود تا ترکیب شیمیایی مورد نظر به دست آید.
3. ریختهگری:
پس از ذوب مواد، فولاد مذاب به قالبهای خاص ریختهگری میشود تا شکل اولیه فولاد زنگ نزن به دست آید. این قالبها میتوانند به صورت شمش، بیلت، یا اسلب باشند.
4. فرآیندهای گرم (عملیات نورد):
فولاد زنگ نزن معمولاً پس از ریختهگری به نورد گرم میرود تا به شکلهای مختلف مانند ورق، میلگرد، لوله و … تبدیل شود. در این مرحله، فولاد گرم میشود و از میان غلتکها عبور میکند تا ضخامت و ابعاد مورد نظر را به دست آورد.
5. فرآیندهای سرد (عملیات کشش و نورد سرد):
در صورت نیاز به بهبود خواص مکانیکی یا سطحی، فولاد زنگ نزن ممکن است وارد مرحله نورد سرد یا کشش سرد شود. این مرحله باعث میشود که فولاد زنگ نزن به ابعاد دقیقتر و سطحی صافتر دست یابد و همچنین استحکام کششی آن افزایش یابد.
6. پوششدهی و عملیات حرارتی:
پس از نورد سرد، ممکن است فولاد زنگ نزن تحت عملیات حرارتی قرار گیرد تا خواص آن مانند سختی و استحکام بهبود یابد. همچنین، ممکن است پوششهای مختلف مانند پولیش کردن، جلا دادن و یا فرآیندهای سطحی دیگر بر روی آن اعمال شود تا مقاومت به خوردگی و زیبایی آن افزایش یابد.
7. کنترل کیفیت:
در تمامی مراحل تولید، آزمایشهای مختلفی برای ارزیابی کیفیت فولاد زنگ نزن انجام میشود. این آزمایشها شامل تستهای شیمیایی، تستهای مکانیکی (مانند کشش و سختی) و تستهای ضد خوردگی هستند. علاوه بر این، بازرسیهای ظاهری برای اطمینان از یکنواختی سطح نیز انجام میشود.
8. بستهبندی و حملونقل:
در نهایت، پس از اتمام فرآیندهای تولید و کنترل کیفیت، فولاد زنگ نزن به اشکال مختلف بستهبندی شده و آماده ارسال به بازار یا مشتریان میشود.
جمع بندی
فولاد ضد زنگ (استنلس استیل) نوعی فولاد آلیاژی است که به دلیل ترکیب حداقل 10.5 درصد کروم، دارای مقاومت بالا در برابر خوردگی و زنگزدگی است. این ویژگیها به فولاد ضد زنگ اجازه میدهد در صنایع مختلف مانند خودروسازی، تجهیزات پزشکی، و صنایع غذایی کاربرد داشته باشد. تولید فولاد ضد زنگ شامل چندین مرحله اصلی است که هرکدام نقش مهمی در ایجاد خواص مطلوب آن دارند.
فرآیند تولید فولاد ضد زنگ با انتخاب مواد اولیه آغاز میشود، که شامل آهن، کروم، نیکل و دیگر عناصر آلیاژی است. سپس در مرحله ذوب و ریختهگری، مواد مذاب به آلیاژ فولاد ضد زنگ تبدیل میشوند و به قالبهای مورد نظر ریخته میشوند. پس از آن، فولاد مذاب به نورد گرم و در برخی موارد نورد سرد وارد میشود تا به شکلهای مختلفی مانند ورق، لوله و میلگرد تبدیل شود.
در نهایت، فولاد ضد زنگ تحت عملیات حرارتی قرار میگیرد تا خواص مکانیکی آن بهبود یابد. سپس با انجام تستهای کنترل کیفیت، ویژگیهای شیمیایی و مکانیکی فولاد بررسی میشود تا از مطابقت آن با استانداردهای مورد نیاز اطمینان حاصل شود. این فرآیندها در کنار هم، فولاد ضد زنگ با ویژگیهای مقاومتی بالا و مناسب برای کاربردهای صنعتی تولید میکنند.
شرکت ساپراویسمن
سوالات متداول
-
فولاد ضد زنگ چیست؟
فولاد ضد زنگ آلیاژی است که حداقل 10.5 درصد کروم دارد و مقاومت بالایی در برابر خوردگی و زنگ زدگی دارد. - چرا فولاد ضد زنگ مقاوم به خوردگی است؟
به دلیل وجود کروم، یک لایه محافظ اکسیدی بر روی سطح فولاد تشکیل میشود که از خوردگی جلوگیری میکند. - روش تولید فولاد ضد زنگ چیست؟
تولید فولاد ضد زنگ شامل مراحل انتخاب مواد اولیه، ذوب و ریختهگری، نورد گرم و سرد، عملیات حرارتی و کنترل کیفیت است. - فولاد ضد زنگ در چه صنایعی کاربرد دارد؟
از فولاد ضد زنگ در صنایع مختلفی مانند ساخت لوازم آشپزخانه، تجهیزات پزشکی، خودروسازی، و صنایع شیمیایی استفاده میشود. -
تفاوت فولاد ضد زنگ آستنیتی و فریتی چیست؟
فولاد ضد زنگ آستنیتی دارای نیکل و کروم بیشتر است و مقاومت بالاتری در برابر خوردگی دارد، در حالی که فولاد فریتی حاوی مقادیر کمتری نیکل است و معمولاً در دماهای بالا استفاده میشود.
هنوز کسی نظری نداده! اولین نفر باش...